Current Industry Challenges in DfMA: Collaboration and Beyond
- Mahdiar Gh
- Jan 20
- 2 min read
Updated: Jan 27
The construction industry is on the cusp of a transformative shift, but it continues to grapple with numerous challenges that hinder the adoption of modern methodologies like Design for Manufacture and Assembly (DfMA). These challenges are not merely technological; they are deeply embedded in the industry's structure, culture, and processes. In this post, we delve into the primary pain points affecting collaboration, communication pipelines, and process inefficiencies, offering insights into why a comprehensive overhaul is necessary.
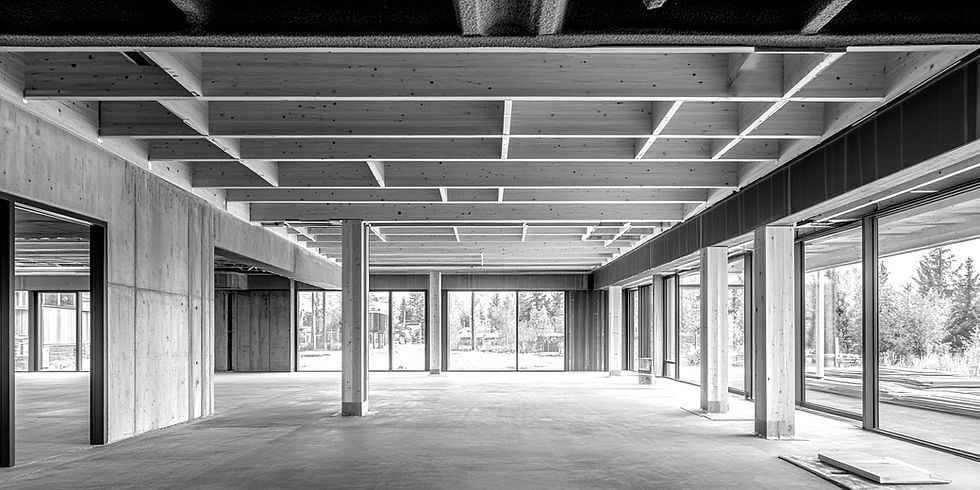
[Research at XOIA Studio: https://www.xoia.ca/services-research]
The Hypothesis: Room for Improvement
Our research began with a straightforward hypothesis: current collaboration procedures in construction projects have room for improvement. The intent was to identify areas of friction in digital collaboration processes and define better pipelines that could support the transition to DfMA. However, what we uncovered was a much more intricate web of inefficiencies and barriers to DfMA adoption.
Key Challenges Identified
1. Collaboration Challenges
The most significant pain points revolve around collaboration. These include:
Inefficient Communication Pipelines: Poorly structured communication channels between stakeholders lead to delays, errors, and wasted effort.
Asymmetry of Effort and Benefits: Upstream design teams expend significant effort creating detailed models, yet the primary benefits are realized downstream by contractors and fabricators. This misalignment of incentives discourages the adoption of collaborative practices.
Lack of Early Engagement: Manufacturers and contractors often join the design process too late, resulting in rework, inefficiency, and missed opportunities for optimization.
Protective Contractual Relationships: Risk-averse contracts often inhibit open collaboration and information sharing.
2. Structural and Cultural Barriers
The construction industry operates on legacy systems that are incompatible with modern methods of construction. These include:
Traditional Project Delivery Models: Methods like Design-Bid-Build limit opportunities for integrating DfMA principles early in the design process.
Limited Manufacturing Knowledge: Designers often lack insight into manufacturing constraints, leading to inefficiencies and higher costs.
Inadequate Knowledge Transfer: There is insufficient transfer of expertise from manufacturers to designers, clients, and contractors.
3. Market Uncertainties
Adopting DfMA requires confidence from all stakeholders, yet several uncertainties persist:
Supply and Demand Imbalances: Clients are hesitant to invest in DfMA platforms without proven scalability, while suppliers are cautious about developing pipelines without guaranteed demand.
Interoperability Concerns: Many DfMA providers use closed, proprietary systems, creating apprehension among clients about being locked into a single platform.
Cost Perceptions: DfMA's focus on early coordination and planning redistributes costs to earlier project phases, creating the perception of higher overall costs.
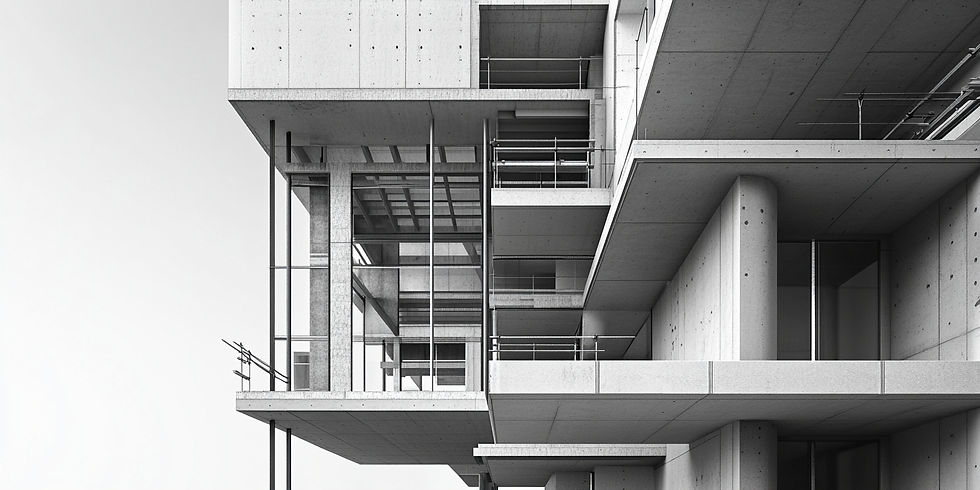
The Call for Change
Addressing these challenges requires more than the implementation of new standards or digital tools. It demands a fundamental rethinking of the industry's structure, processes, and cultural norms. The benefits of DfMA—efficiency, sustainability, and cost-effectiveness—can only be realized through targeted change management efforts that foster collaboration, early engagement, and knowledge sharing.
Acknowledgment
This blog post is informed by research conducted as part of the Researcher-in-Residence program at Perkins and Will. Special thanks to the Vancouver and Calgary studios, my co-researcher Elton Gjata, and the advisory committee (Yehia Madkour, Kathy Wardle, Andrew TsayJacobs, Adrian Watson) for their invaluable contributions.
Comments